To answer a couple of questions from yesterday;
Dave, those brass ground plates aren't for sale anywhere I know of, I have made my own in the past from light gauge brass plate bought at the hardware store.
Bassman, Yeah, that's Gabes drawing, this week I'm posting some interesting posts from the old board that I've saved.
I wokle up this morning to find these, looks like my daughter was up all night making goodies.
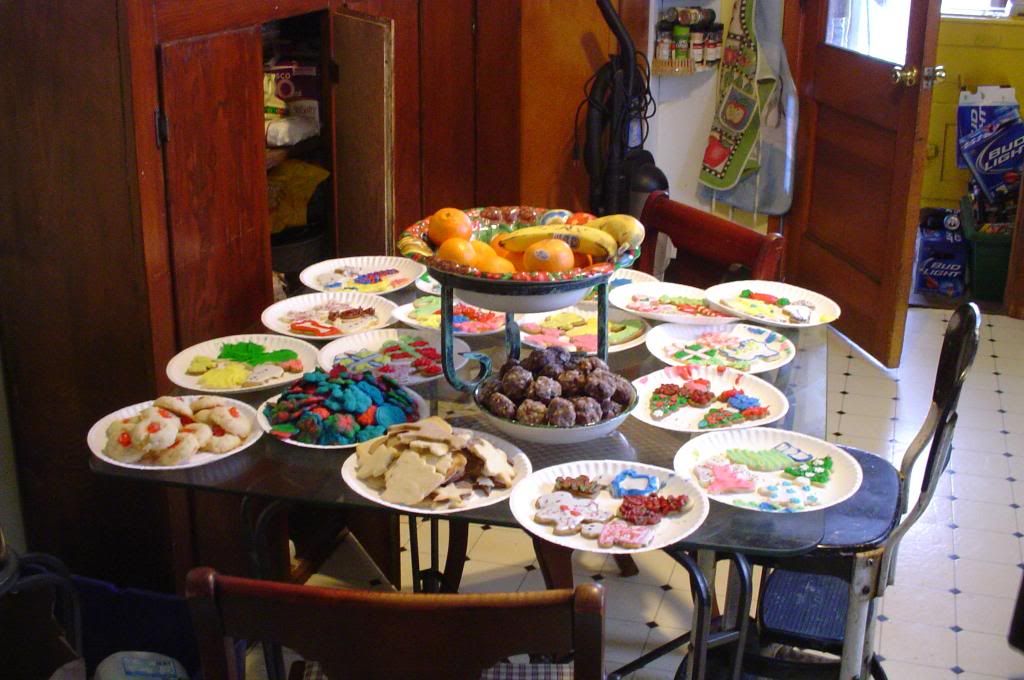
I've played the ASAT Clasic for a week and a half now and I do like it a lot but it still ain't no 500! Post a pic of your #1 guitar or bass.
Of the four 500's I have this one was the first and it's still the best.
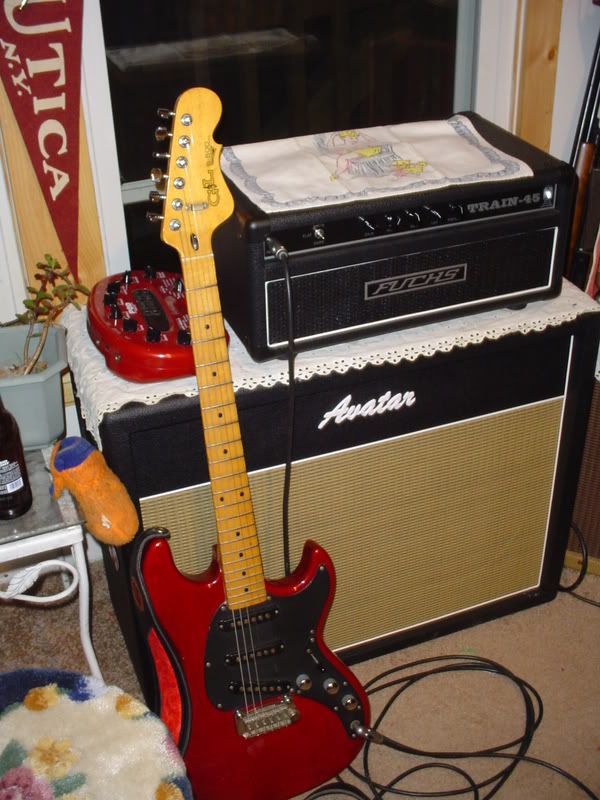
MY #1 bass
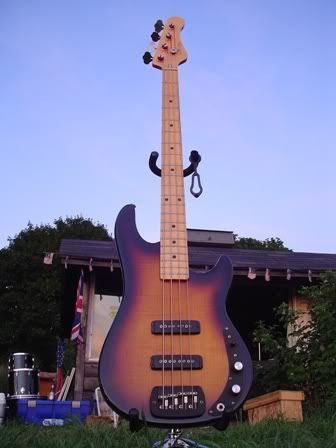
#1 Amp, that's a tough one, like a Morman loves all his wifes for different reasons I love all my amps.
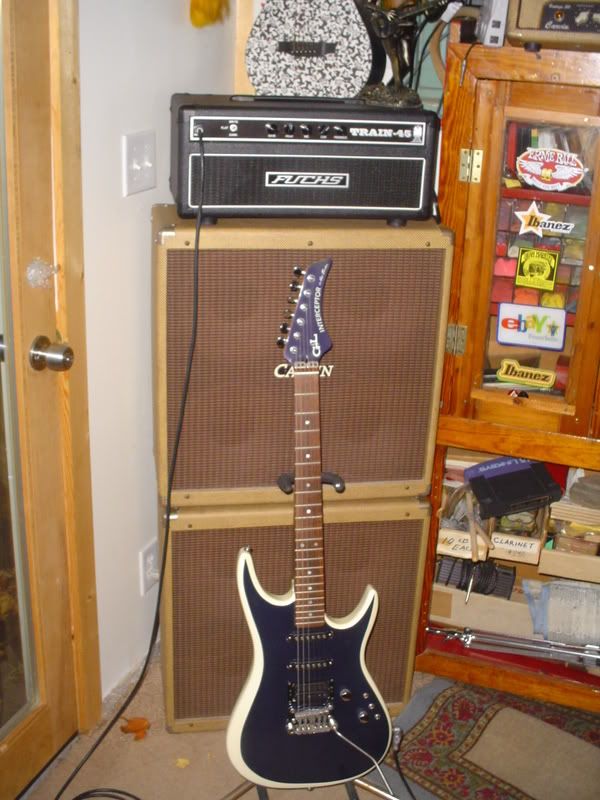
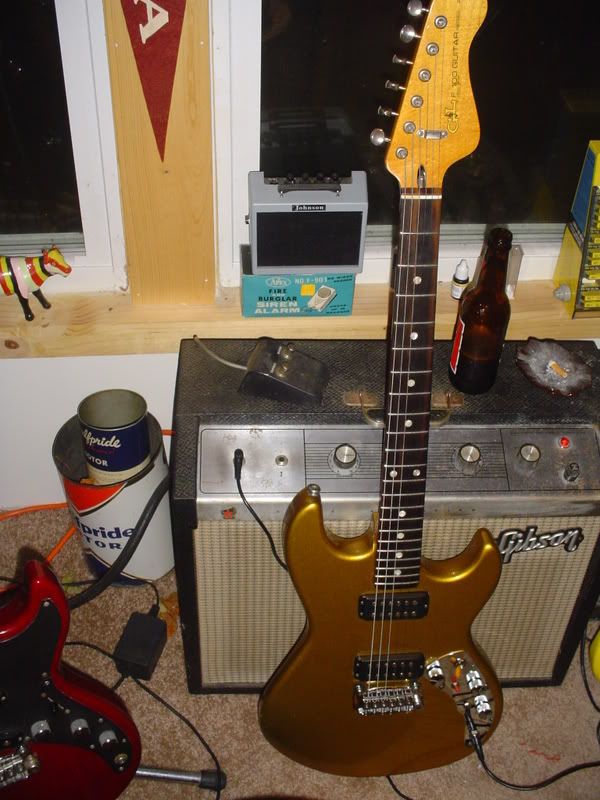
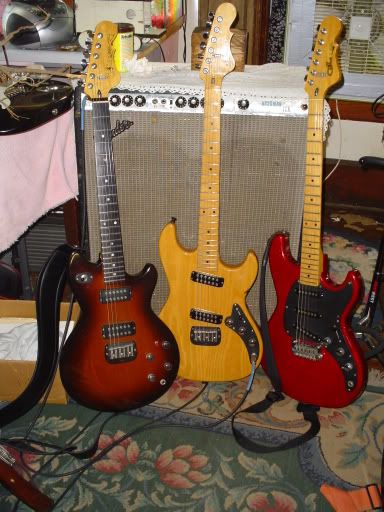
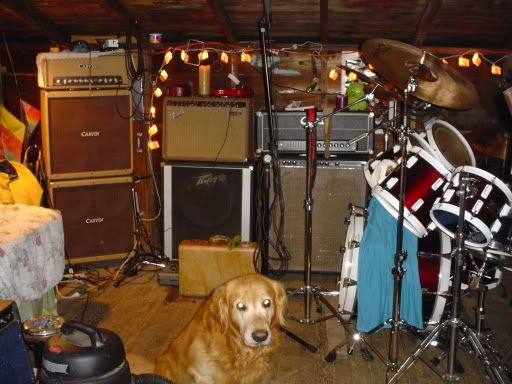
one of my bass riggs
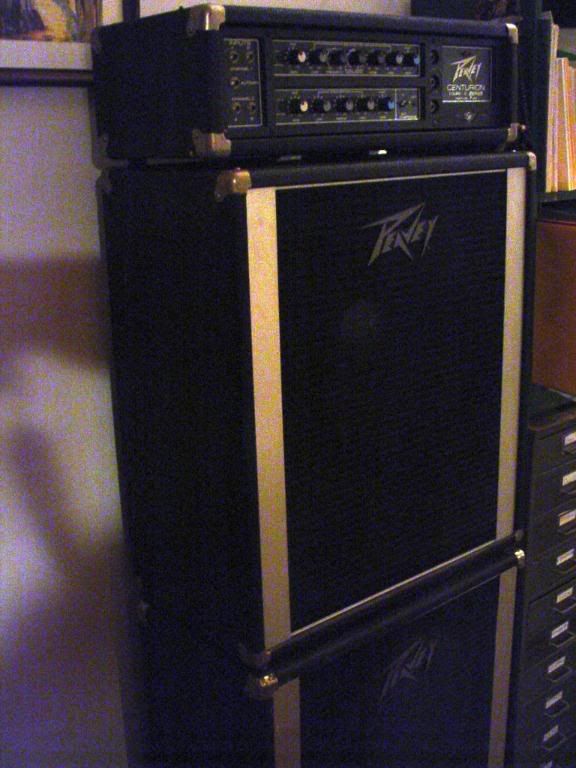
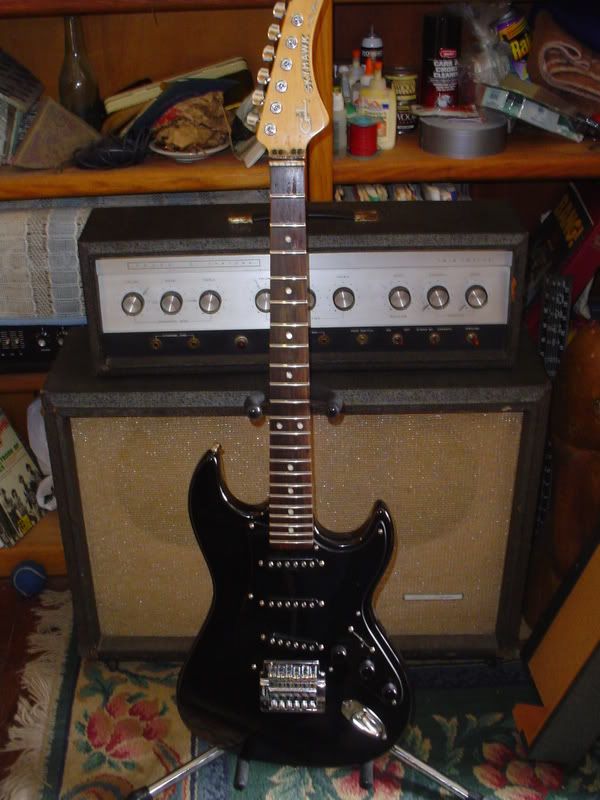
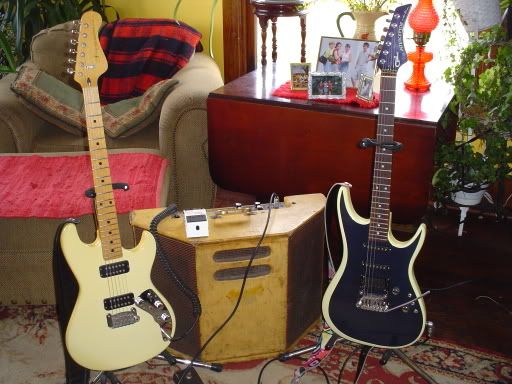
The Silvertone guitar and bass amps
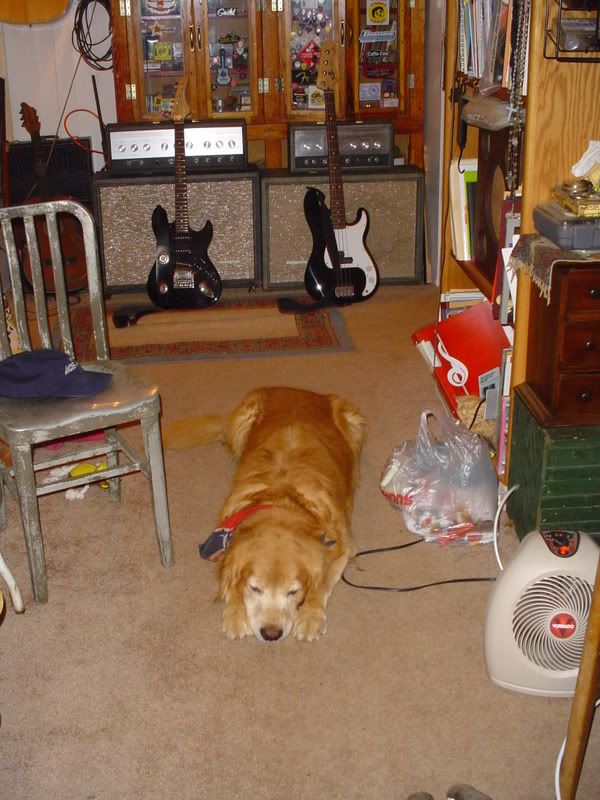
What other toys you gott? post em up I like car and truck pics if you got em, anything motorized!
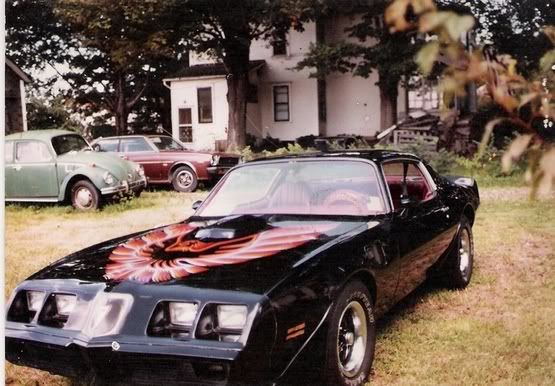
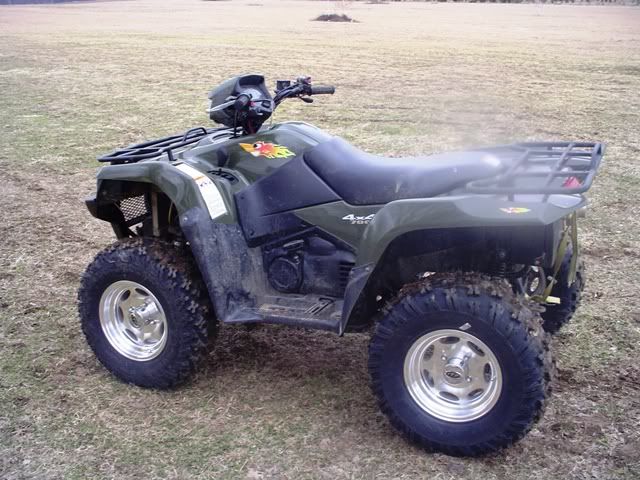
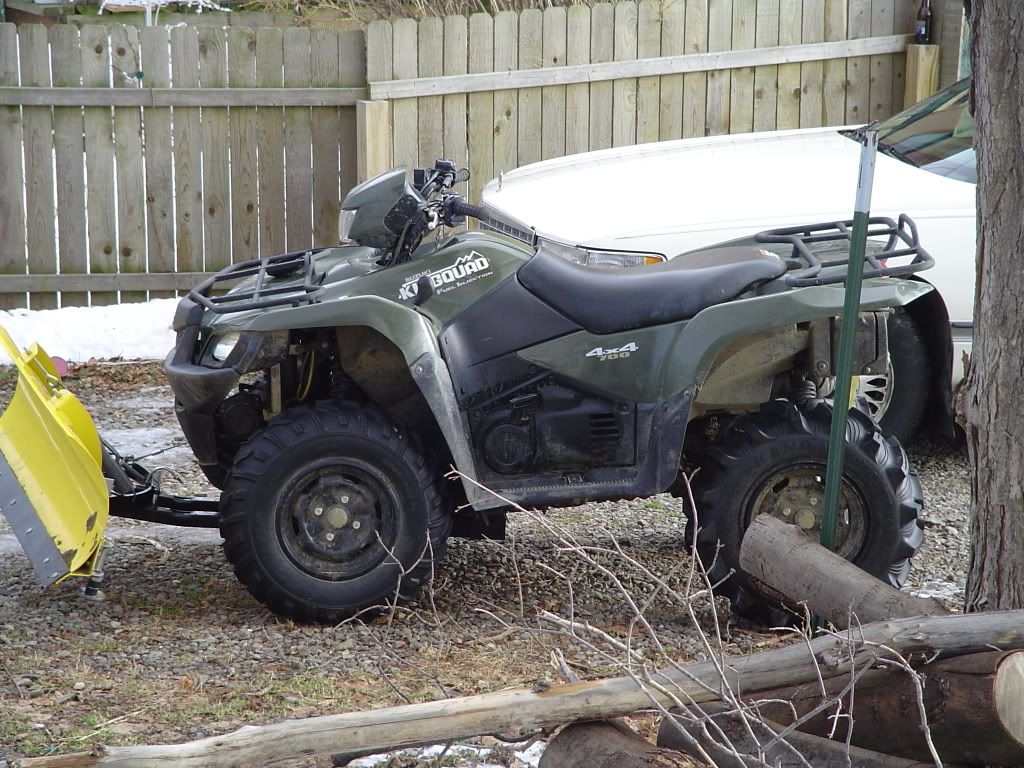
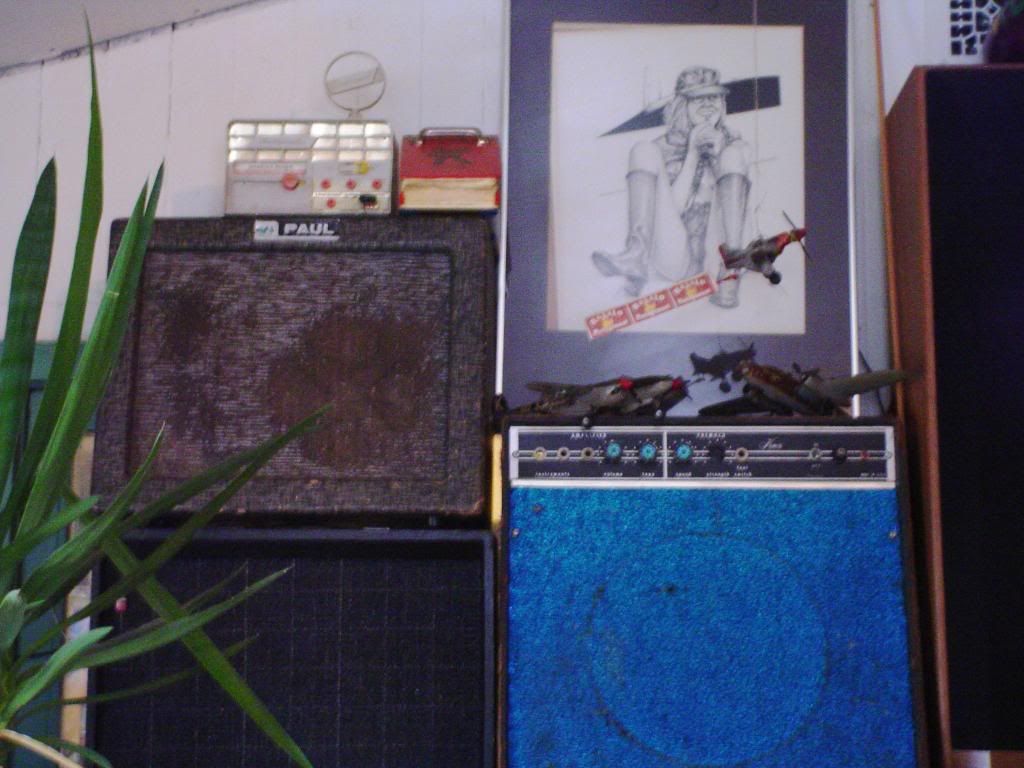
Your TID BITS from the past for today is an article by Greg G. regarding Fender after Fender, this one covers the Fender Custom shop, unfortunatly I never saved part two covering the G&L era, maybe if Greg is lurking he can post up part two!
Thanks Greg
G&L content for today and tomorrow will be a 2-part article I co-authored about 6 or 7 years ago regarding Leo Fender's companies after he left them. Naturally, G&L will be included (in part 2). Please don't be put off by the fact that part 1 is about the Fender Custom Shop as it will give you better perspective on how things are (were) at G&L.
Leo’s Legacy, Part 1: Fender after Fender
By Greg Gagliano and Tim Pershing
Without doubt, Leo Fender was the most influential designer and manufacturer of electric solid body guitars and amplifiers in the 20th century. During his career he worked at and owned several companies. The first, K&F (1945 – 1946), was a small operation jointly owned by Leo and Doc Kaufmann. This short-lived venture produced amps and lap steels, and was the springboard for the Fender Electric Instrument Company (1946 - 1964) – Leo’s most famous endeavor.
After the sale of FEI to CBS in 1965, Leo was contractually forbidden to make guitars and amps for a 10-year period. After this period expired, Leo joined forces with Forrest White and Tom Walker at Music Man (1975 - 1980). Conflict at Music Man was the catalyst for Leo to break from that company and form his last venture, G&L (1980 - 1991), with George Fullerton.
We wanted to know what has been happening at Leo Fender’s former companies and with his guitar designs now that he is quite “removed” from the picture… or is he? All three corporations, Fender, Music Man and G&L are in the hands of capable owners and doing quite well. Leo’s designs continue to influence these businesses (to some extent) and we inquired to what degree that these companies are able to operate “unencumbered” by Leo’s legacy. Part 1 of this series looks into the Fender Custom Shop and how the people there view Leo’s legacy.
We’ve chosen the Custom Shop (as opposed to the regular production facility) for a variety of reasons. For one, better comparisons with Music Man and G&L are possible, thanks to their smaller scale of production. And the best connections with Leo-era Fender can be found in the Custom Shop (both in the workforce, several of whom actually worked at FEI, and in the guitars themselves – which are beginning to blur the line between vintage and reproduction).
The Custom Shop was established in 1987 to produce custom-built guitars and high-grade production instruments. A lot of people think of a Custom Shop guitar as either a Relic or a super fancy “one off” with a gazillion inlays. However, much of what they do we don't see, such as super accurate vintage models (and I mean SUPER accurate, to please even the most anal-retentive vintage snob – the authors included), dealer specific models, artist models, and wild/weird/wonderful R&D projects.
The shop currently employs about 50 people and is located in sunny Corona, California (approximately 20 miles east of the original Fender factory in Fullerton). The Custom Shop and regular production facilities were originally housed in separate buildings about 1 mile apart, but have recently moved into a single building within the same industrial complex.
There are three main product lines manufactured in the Custom Shop: Master Built, Master Grade, and Production. Individual master craftsmen produce the Master Built Series instruments. There are approximately nine Master Builders (plus assistants) at the Custom Shop. This group has its own R&D, marketing and artist relations departments. The Master Built guitars represent the finest instrument that Fender has to offer and are a significant departure from the assembly line instruments manufactured by FMIC.
These guitars are made with much handwork, though some wooden parts are occasionally made using a CNC milling machine. They range in style from vintage reissues to avant-garde non-traditional models. Examples of these models include the “pieces of art” that have been featured in articles (and Fender ads) in all the guitar rags. Fender has also issued a coffee table picture book detailing some of the Custom Shop creations (and creators) as well as a popular 12 month calendar.
The Master Grade Series instruments were made exclusively for Yamano, a distributor in Japan, but beginning in 1999 this series will be offered in the US as well. These guitars are extremely accurate reissues of vintage Fender models that satisfy the most demanding vintage enthusiasts in Japan. The accuracy of these reissues defies explanation and the Japanese distributor is so demanding that it sometimes rejects a very small percentage of these guitars as not being “perfect enough.” The NOS ’65 Stratocaster model (introduced in 1998) has its roots in the Master Grade series.
The Production Series guitars are standardized models made by a team of about 40 workers. This line includes the Relic line of guitars, which are the Custom Shop’s most popular models, and the various ‘50s and ‘60s high-end reissue lines. As on all Custom Shop instruments, the materials used for the Production Series models are of a higher grade and quality than found on standard FMIC models. This requires the Custom Shop to select and purchase its own materials. The Production series and regular production line guitars at FMIC share the same R&D department.
Fender is a huge company and it certainly is not the same enterprise that Leo had going in the 1950s and early 1960s. Nor is it the same company that was owned by CBS. However, the Fender Custom Shop is clearly making its finest products since the days of Leo Fender. It can be argued that the quality of these small-run production and hand-made guitars exceeds anything that FEI was able to do, though players will always bestow “vibe” where they see fit! There is no argument however that the new owners brought the company out of the darkest days of the CBS-era (in the mid-1980s) into the place of prominence that they enjoy today.
It is clear that the Fender Custom Shop is neither constrained nor hindered by Leo’s legacy. Philosophically, the Custom Shop is still guided to some extent by Leo's legacy. Witness the vintage models that are a huge part of the Custom Shop line. Though it would be very easy to exclusively use modern manufacturing techniques, the Custom Shop uses technology on an as-needed basis. In fact, much of the work performed is done just as it was at FEI and FMI… by hand. To some extent, the craftsman work areas resemble those from FEI pictured in Richard Smith’s book (Fender: The Sound Heard ‘round the World), though the Custom Shop has a decidedly modern and “neat” feel to it.
While touring the production facilities and admiring the skill of handwork being performed, we wondered how many of the employees were familiar with Fender’s history (remembering that many of them weren't even born when Leo started the company). Most of workers we spoke with were well aware of Leo’s contributions and designs and are gratified to be a part of his legacy. Some had very close ties to the man. Geoff Fullerton, son of George Fullerton, works in the Custom Shop along with Abigail Ybarra and Herbie Gastelum.
Abigail has been winding pickups since 1957 and Herbie has been shaping necks since 1961. Unbelievable! Incidentally, co-author Tim Pershing discovered a “HERB G.” inspection stamp in his ’74 Musicmaster which is attributable to Mr. Gastelum! We asked them a very direct question... one which they easily could have given us the "right" answer... but one which they answered with honest sincerity. We asked if they felt that the Custom Shop does the work similarly to the way it was performed in the old days, and if Mr. Fender would have approved. They each gave us a resounding "YES!" to both parts of the question. Leo's legacy is alive and well at the Custom Shop, folks.
Regardless of their knowledge of Fender history, the craftspeople at the Custom Shop obviously care about the work they do and the guitars they build. Every worker was proud to hand us what they were working on, be it a pickup, a neck, or whatever. Despite the Big Bad Corporation image that Fender sometimes gets (rightly or wrongly), we can assure you that the people who make the Custom Shop guitars really care about making you (us, musicians, collectors, whatever) proud to own and play their products. Yes, the designs are classics that have been proven over the test of time, but it is the PEOPLE making the guitars today that really count.
Fender after Leo Fender is flourishing, and our visit to the Custom Shop has greatly reassured us that his spirit of invention and quality are very much alive and well. The authors wish to thank Mark Duncan for being their tour guide through the Custom Shop. Also, thanks to John Page, John Grunder, and all the craftspeople at the Fender Custom.
See you all tomorrow and post up them pics
gary